在半導體、新能源等行業(yè)的加速迭代中,大型冷熱沖擊試驗箱的運行頻率從每日 10 次循環(huán)提升至 30 次以上,工況下甚至達到每小時 1 次的高頻沖擊。這種高頻運行使得設備結構長期承受溫度應力與機械載荷的交替作用,傳統(tǒng)的局部加固、焊點補強等淺層優(yōu)化手段已難以抵御疲勞失風險。真正可靠的解決方案,需要構建從材料選型到整體結構設計的全維度抗疲勞體系。
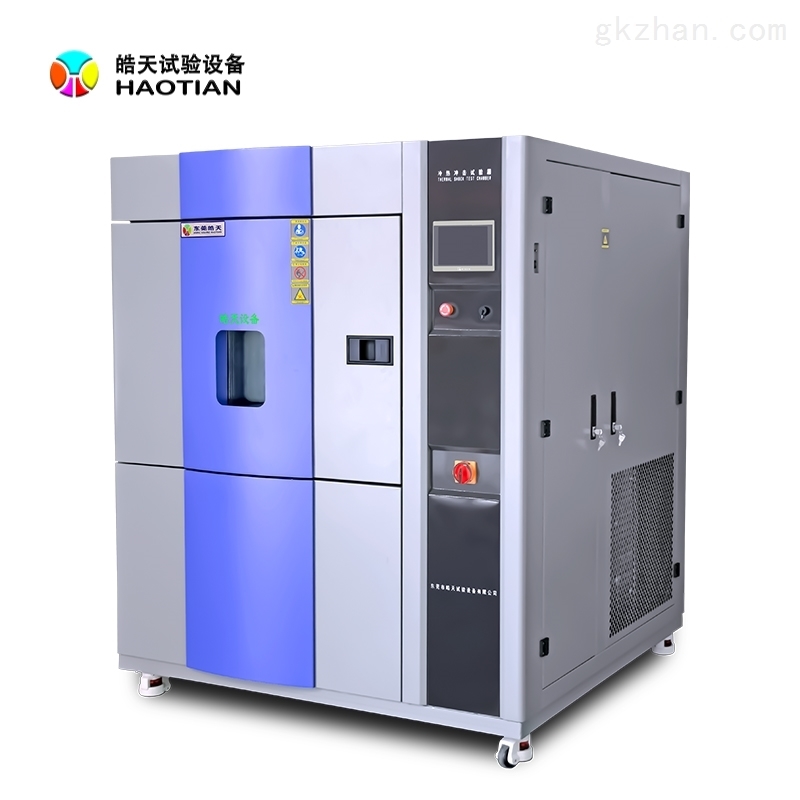
高頻運行下的疲勞失效機理遠比想象中復雜。箱體框架在 - 70℃至 150℃的溫度沖擊下,每循環(huán)一次會產生 0.12mm/m 的線性伸縮量,這種周期性形變在螺栓連接部位形成高達 180MPa 的交變應力。某汽車零部件測試中心的數(shù)據(jù)顯示,采用普通 Q235 鋼螺栓的試驗箱,在 2000 次高頻循環(huán)后,83% 的連接點出現(xiàn)螺紋塑性變形,其中 3 處發(fā)生斷裂。更隱蔽的是焊接部位的疲勞累積,冷熱交替產生的微裂紋會以每月 0.02mm 的速度擴展,在 6000 次循環(huán)后可能突然引發(fā)箱體滲漏。
突破局部優(yōu)化局限,首先需要材料體系的革新。箱體主框架采用低溫韌性優(yōu)異的 Q355ND 低溫鋼,其 - 40℃沖擊功≥34J,配合時效硬化處理,可使材料疲勞強度提升 40%。關鍵承重部件則選用 17-4PH 沉淀硬化不銹鋼,經(jīng) H900 熱處理后,抗拉強度達 1310MPa,在 100 萬次應力循環(huán)下的疲勞極限比傳統(tǒng) 304 不銹鋼提高 58%。某光伏測試設備的對比試驗表明,采用新型材料體系的箱體,在 1 萬次高頻循環(huán)后結構變形量控制在 0.3mm 以內,僅為傳統(tǒng)結構的 1/5。
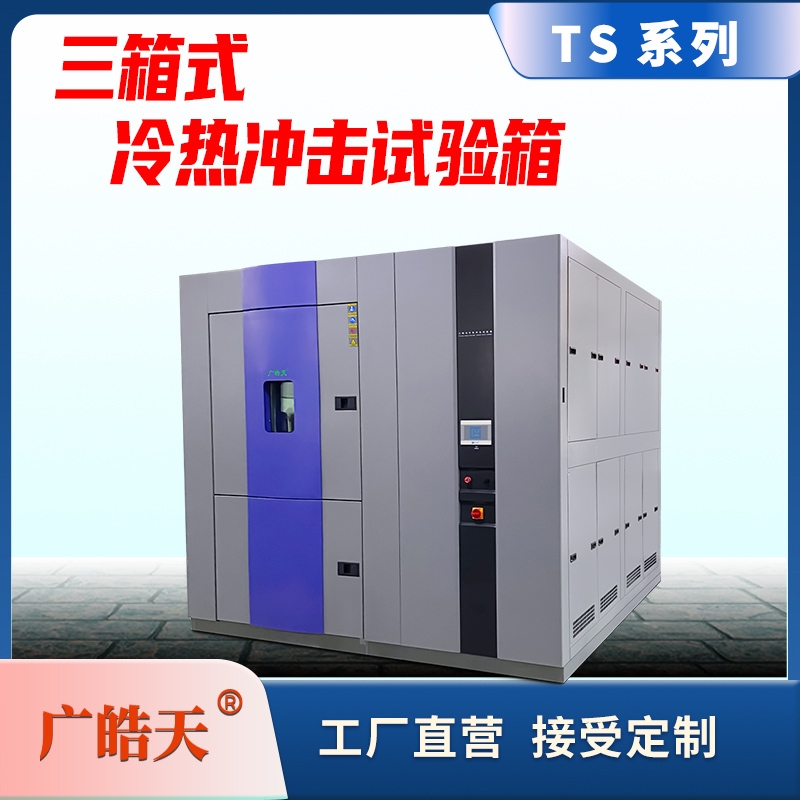
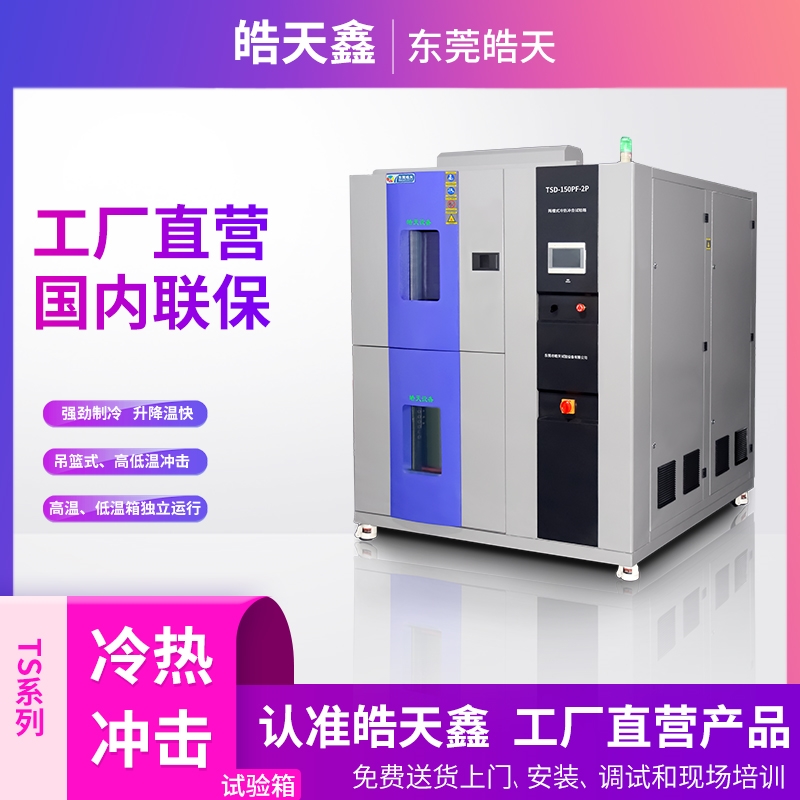
整體結構的拓撲優(yōu)化是抗疲勞設計的核心。通過有限元分析軟件對箱體進行 120 萬次循環(huán)模擬,識別出應力集中系數(shù)>3 的危險區(qū)域,采用變截面設計將拐角部位厚度從 8mm 漸變至 12mm,使應力分布均勻性提升 62%。鉸鏈與門鎖系統(tǒng)采用四點懸浮式連接結構,通過聚四氟乙烯墊片的彈性緩沖,將交變載荷衰減 35%,實測顯示其疲勞壽命從 5000 次延長至 2 萬次以上。
動態(tài)應力監(jiān)測系統(tǒng)的引入實現(xiàn)了疲勞風險的主動防控。在箱體側壁、門體框架等 6 個關鍵部位植入光纖光柵傳感器,實時監(jiān)測應力變化曲線,當檢測到應力幅值超過材料疲勞極限的 80% 時,自動觸發(fā)降頻保護程序。某航空航天實驗室的應用案例證明,該系統(tǒng)可使突發(fā)性結構失效的預警準確率達到 97%,將維護成本降低 60%。
抗疲勞技術的目標是實現(xiàn)全生命周期的可靠性。通過數(shù)字孿生技術構建的虛擬試驗模型,能夠精準預測不同運行頻率下的結構疲勞壽命,為用戶提供個性化的維護周期建議。數(shù)據(jù)顯示,采用系統(tǒng)抗疲勞方案的試驗箱,在每日 30 次循環(huán)的高頻運行下大修周期可延長至 5 年,比局部優(yōu)化方案提升 2 倍以上,解決了高頻運行與結構可靠性之間的矛盾。